Sunday, May 31, 2009
Vintage 1950's Leach Video
Enjoy!!!
Friday, May 29, 2009
Not a great week... but good



I’m rather particular on their fit, so I usually throw quite a few more than I need and toss what’s not used in to my reclaim bucket. I revisited the lid making process for a new local blog I’m playing with. If you haven’t seen how I make my lids yet, take a quick look. It’s one more approach the making a lid.
Sunday, May 24, 2009
Creating a Paper Stencil Part 2
The first part is in the previous post. It shows the technique I use for cutting out 30 to 40 stencils at a time. I do this by cutting my design out of a billet of newsprint sandwiched between sheet plastic using a jewelers saw and bench pin. I can actually get 60 to 80 stencils out a a single billet if I plan my design around the cut, using both the positives and negitves in a design.
This clip shows how I apply the stencils to create a composition. It goes on to show the slip being applied and the paper being peeled away revealing the surface design.
Enjoy!
Saturday, May 23, 2009
Creating a Paper Stencil Part 1
This demo is divided into 2 parts. I know I have a hard time sitting still longer than 4 minutes, so I've tried to keep each clip relatively short.
I've got lots of question marks with these videos, but my big question right now is... Does it need sound? I have my stereo blasting Miles Davis and Trombone Shorty while I'm sitting around slapping these videos together, so I assume that everyone else sitting at their computer has their own trax playing in the background.
Self doubt and second guessing always seems to lurk in the shadows, luckily it rarely keeps me from having fun!
Laguna Clay Gallery
This week there have been grants accepted, pedestals made, forums found, new friends made, a kiln load readied, gardens planted, sales made, a public bronze pour, throwing demos, lots of new works thrown, and I got accepted into the Laguna Clay Gallery! I'm right after Yoshiro Ikeda. I'm very last in the line-up... COOL!
I really want to thank Jim Gottuso for cluing me into this oppertunity. His work is truly inspirational!
WoW! No picts this time? What's up with that!
Sunday, May 17, 2009
Cone 6 SDSU Texture & Crawl Glaze

25% Magnesium Carbonate
70% Nepheline Syenite
5% Kentucky Ball Clay (OM4)
This is the basic recipe of the crawl glaze that I've been playing with over the past few months. I found it buried in an old sketchbook scrawled in a corner of a page. It was from 8 or 9 years ago during a time when I didn't have any sort of studio access and was sucking up as much information as I could get my hands on. The recipe is attributed to a October 2000 Ceramics Monthly article on page 49, unfortunately I failed to note who the author was. (Hopefully someone can help me rectify that.)
This glaze is very temperamental and you need to place it in the kiln asap after dipping. The glaze will crack and begin to pull away but not quite fall... unless it's disturbed. It's very sensitive to thickness.The glaze will behave very differently based on what's under or over it.
Here's a link to a February post showing some of my experiments... http://fetishghost.blogspot.com/2009/02/test-yumoni-for-crawling-glaze.html
Experiment and have fun and please share any successes or failures you have.
Thursday, May 14, 2009
Throwing AgateWare Yunomi
This is a short stop motion animation video the kids and I shot last weekend demonstrating the throwing of an "agateware" yunomi. This is a simple process of throwing two contrasting clays together to create a marvelously swirled effect directly in the clay body. I finally got around to pasting together a first draft to share....
Wednesday, May 13, 2009
Raku with Bruce





Another fun day spent with Bruce Cadman.

Man... I think that this guy really needs to wear a cape and mask, he seems to have way too much fun!
He did let me put in a piece in the raku kiln to see what might come out. I just sat back and took pictures…
Saturday, May 9, 2009
Crawl and Soda
Thursday, May 7, 2009
Hands in Clay Exhibition
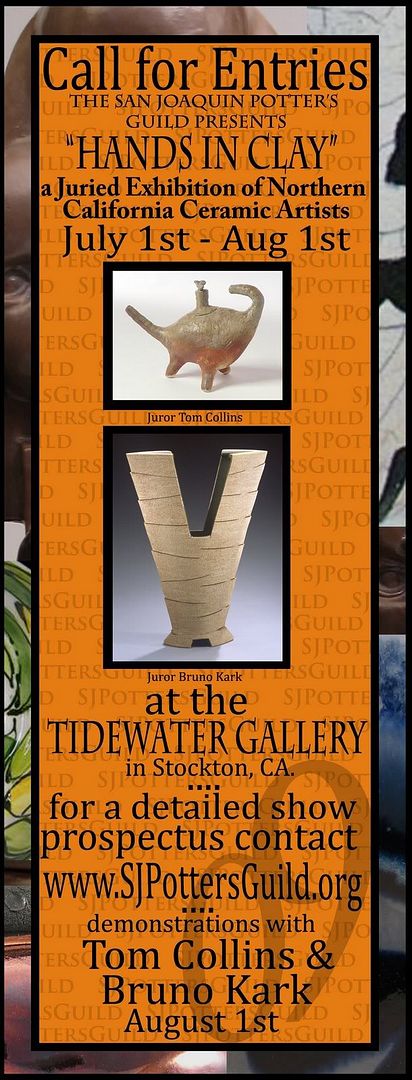
When times look blue what do you do?
Monday, May 4, 2009
A Quick Look in the Box

Sunday, May 3, 2009

